Ablaufplanung der Prozess- und Durchführungsplanung
Nachdem das Produktionsprogramm nach Art und Menge festgelegt wurde muss die optimale Größe des Fertigungsauftrags (Menge) definiert werden (siehe Losgrößenplanung der Prozess- und Durchführungsplanung – Brain365)
Nach der Festlegung der optimalen Größe eines Fertigungsauftrags, in Form der Losgröße erfolgt die eigentliche Feinplanung. In dieser Feinplanung wird die kostenminimale Ausführung der Fertigungsaufträge unter Beachtung vorgegebener Fertigstellungstermine angestrebt.
Um die Produktion effektiv zu steuern werden in der Produktion unterschiedliche Ziele verfolgt. Hierzu gehören
- Minimierung der Durchlaufzeiten (DLZ) aller Aufträge
- Durchlaufzeiten bei der Ausführung von Aufträgen spielen eine Rolle in der Produktion. Unter Durchlaufzeiten versteht man alle
- Produktionszeiten / Bearbeitungszeiten + Kontrollzeiten (empirischer Anteil 10%+3%)
- Transportzeiten (empirischer Anteil 2%) und
- Wartezeiten / Liegezeiten (empirischer Anteil 85%)
auf allen Produktionsstufen:
- Durchlaufzeiten bei der Ausführung von Aufträgen spielen eine Rolle in der Produktion. Unter Durchlaufzeiten versteht man alle
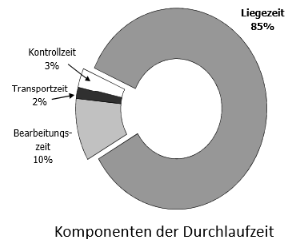
- Wartezeiten (auch Liegezeiten genannt) sind der, zum Zeitpunkt der Ablaufplanung (Feinplanung) beeinflussbare Faktor (i.d.R)
- es wird davon ausgegangen, dass es für die Minimierung von Wartezeiten einen zur Verfügung stehenden Spielraum gibt, denn
- 77 % der Liegezeiten sind arbeitsablaufbedingte Liegezeiten
- 5 % der Liegezeiten machen Lagerungszeiten aus
- 3 % der Liegezeiten sind störungsbedingt
- 0,2 % der Liegezeiten sind, durch den Menschen bedingte Liegezeiten
Rest ist unklar
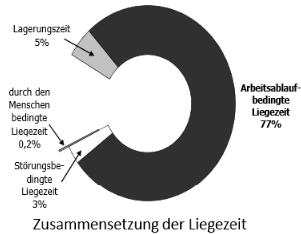
2. Minimierung der Zykluszeiten
- Zykluszeit ist die Durchlaufzeit des am längsten in Bearbeitung befindlichen Auftrags (längste DLZ eines Auftrags) innerhalb einer Menge von Aufträgen = Auftragsbestand,
- d.h. die Zeit zwischen
- Eintreffen der Aufträge (eines Auftragsbestands in der Produktion) und der
- Fertigstellung des gesamten Auftragsbestands (Fertigstellung der gewünschten Produktionsmenge)
3. Minimierung ablaufbedingter Maschinenstillstandszeiten
- Maschinenstillstandszeiten sind ein Teil von Belegungszeiten von Maschinen
- Belegungszeiten sind die Summe aller
- Produktionszeiten
- Rüstzeiten und
- Stillstandszeiten
Der Abbau von Stillstandszeiten von Maschinen liegt im Fokus der Minimierungsbestrebungen und ist i.d.R der zum Zeitpunkt der Ablaufplanung beeinflussbare Faktor.
4. Einhaltung der Ablieferungstermine
- für das Verhältnis zum Kunden ist die Einhaltung von gewünschten und / oder bestätigten Lieferterminen für Kundenaufträge (Ablieferungsterminen) sehr wichtig
- dies ist häufig nur durch teure Sonderaktionen (Sonderschichten, verlängerte Werkbank..etc.) erreichbar. Dies ist sehr kostensensitiv und sollte vermieden werden
Das Dilemma der Produktionssteuerung:
Die vier Ziele
- Minimierung der Durchlaufzeiten (DLZ) aller Aufträge
- Minimierung der Zykluszeiten
- Minimierung ablaufbedingter Maschinenstillstandszeiten
- Einhaltung der Ablieferungstermin
lassen sich i.d.R. schwer gleichzeitig erreichen. Sie sind konfliktär.
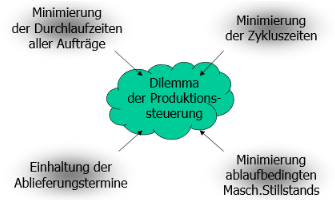
Es gibt bei der Optimierung der Produktion einen eklatanten Zielkonflikt zwischen
Wenn die Durchlaufzeiten kurz sind, dann sind i.d.R. die Maschinenstillstandszeiten lang. Wenn die Maschinenstillstandszeiten lang sind, dann sind die Durchlaufzeiten entsprechend kurz.
Dieser Zielkonflikt wird das „Dilemma der Ablaufplanung“ genannt.
Reihenfolgeplanung bei einem Aggregat
Ziel der Reihenfolgeplanung, unter Berücksichtigung eines Aggregats ist die Minimierung der
- Rüstzeiten oder
- Rüstkosten,
sofern des betrachtete Aggregat der Engpass ist.
In diesem Fall führt die Optimierung der Rüstzeit zu einer Erhöhung der verfügbaren Bearbeitungskapazitäten und somit zu
- zusätzlichen Deckungsbeiträgen.
Wie kann die optimale Reihenfolge der Produktionsaufträge, die zu einer rüstzeitenminimalen und somit kostenminimalen Produktion führt, bestimmt werden?
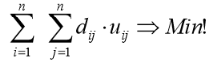
dij: Rüstkosten, Rüstzeiten je Umrüstvorgang von der Produktart i zur Produktart j
uij: Reihenfolgevariable, die den Wert 1 annimmt, falls von der Produktart i auf die Produktart j umgerüstet wird, und den Wert 0, falls dies nicht erfolgt
Idee:
Übertragung der Grundstruktur des „Traveling Salesman Problems“ zur Bestimmung der optimalen Rüstreihenfolge: “ Wie ist die Reihenfolge für den Besuch mehrerer Orte zu wählen, damit die gesamte Reisetrecke des Handlungsreisenden nach der Rückkehr zum Ausgangspunkt möglichst kurz ist?“
Ablaufplanung bei mehreren Aggregaten
Grundproblem der Ablaufplanung bei mehreren Aggregaten ist die Zuordnung von
- n Produktionsaufträgen auf
- m aufeinander folgende Betriebsmittelgruppen.
Optimierungsverfahren (wie z.B. die oben aufgeführte Branch-and-Bound-Methode) scheiden aus, weil somit eine sehr große Anzahl (n! ^m => Anzahl Produktionsaufträgen (n) Fakultät hoch m Betriebsmittelgruppen) Reihenfolgen zu analysieren wären.
Stattdessen werden Prioritätsregeln eingesetzt, um die Reihenfolge der Produktionsaufträge festzulegen:
- Shortest Processing Time (SPT) – kürzeste Operationszeit)
- First Come, First Serve (FCFS) – längste Wartezeit (der Auftrag der zuerst eingeht, wird zuerst abgearbeitet – das ist der Auftrag mit der längsten Wartezeit)
- Longest Processing Time (LPT) – längste Operationszeit)
- Smallest Set-Up Costs (SSC) – geringste Umrüstkosten
- Total Work (TWORK) – größte Gesamtbearbeitungszeit
Jede Prioritätsregel erfüllt die einzelnen Ziele der Produktionssteuerung unterschiedlich, so dass praktisch
- entweder eine gewichtete Kombination verschiedener Prioritätsregeln zum Einsatz kommt
oder - ein Gütetest einzelner Prioritätsregeln mittels Simulation stattfinden muss:
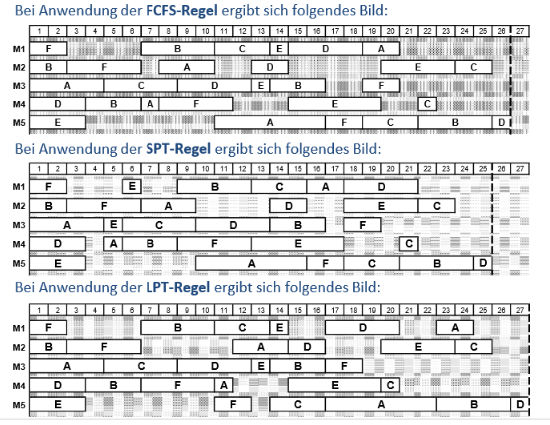
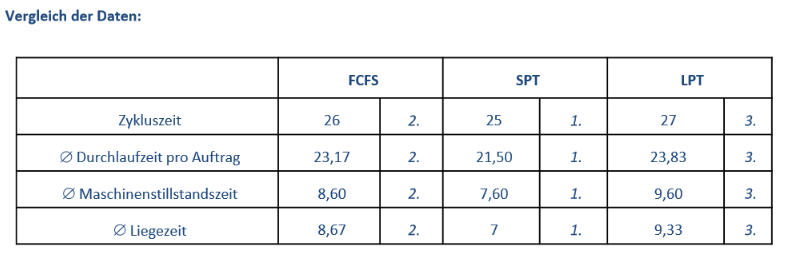
Betrachtet man die Erfüllung der Ziele anhand der einzelnen Aufträge, so ergeben sich insbesondere für die Aufträge C und D „schlechte“ Ergebnisse.
Bereits dieses kleine Beispiel zeigt auf, wie komplex die Entscheidungen bzgl. der Reihenfolgeplanung ausfallen können.
Bedenkt man, dass die unterschiedlichen Zielsetzungen der Produktionssteuerung im Allgemeinen von verschiedenen Funktionsbereichen bzw. Personen im Unternehmen vertreten werden (Vertrieb, Technik, Fertigung, Controlling etc.), so wird die Notwendigkeit deutlich,
sich zunächst auf eine Priorität der Ziele zu einigen, um anschließend die Maschinenbelegung durchführen zu können.
Über Advanced Planning Systeme, APS-Module in ERP-Systemen oder MES-Systemen lässt sich eine Feinplanung und Simulation der Ablaufplanung effizient durchführen. Die Effizienz einer solchen Planung basiert auf den grundlegenden Basisdaten, sowie der Grobplanung, die in übergeordneten ERP-Systemen durchzuführen ist.